How to Implement a Dropped Objects Prevention Plan – Part 3
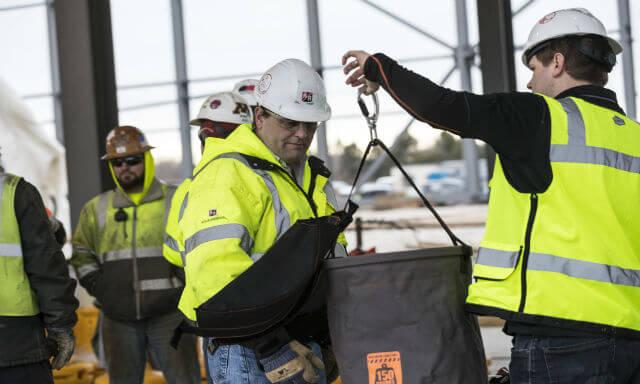
The following is the third post in a four-part series on implementing a dropped objects prevention program. In part three, we’ll focus on executing the controlled implementation and policy creation of your program. If you missed Part 1 or 2, you can read them here: How to Implement a Dropped Objects Prevention Plan – Part 1 and Part 2.
Like climbing ladders or stairs, there are steps to take to implement a dropped objects prevention plan on your jobsite. Regardless of industry, your roadmap to a successful dropped objects program should be:
- Call to Action
- Identify Risk & Define Scope
- Observation/Site Assessment
- Training
- Controlled Implementation
- Policy Creation
- Launch
- Review & Expand
CONTROLLED IMPLEMENTATION
Once you’ve observed your site and trained your workers, you’re ready to roll out your dropped objects plan in the pilot area that you identified in steps two and three. Analyze your findings from the observation and assessment of your pilot area that you should have completed. Utilize a Hazard Identification & Analysis tool to document these observations. But you don’t want to do this haphazardly and skip a step. Work through the hierarchy of controls to identify holistic controls based on your known hazards.
Can any hazards be outright eliminated? Or if not, can you substitute any unsafe conditions, equipment or materials to replace the hazard? If the answer is yes, then fix any unsafe conditions found. Examples include moving any unnecessary work at heights and setting up process on the ground, replacing corroded or damaged equipment and eliminating poor housekeeping.
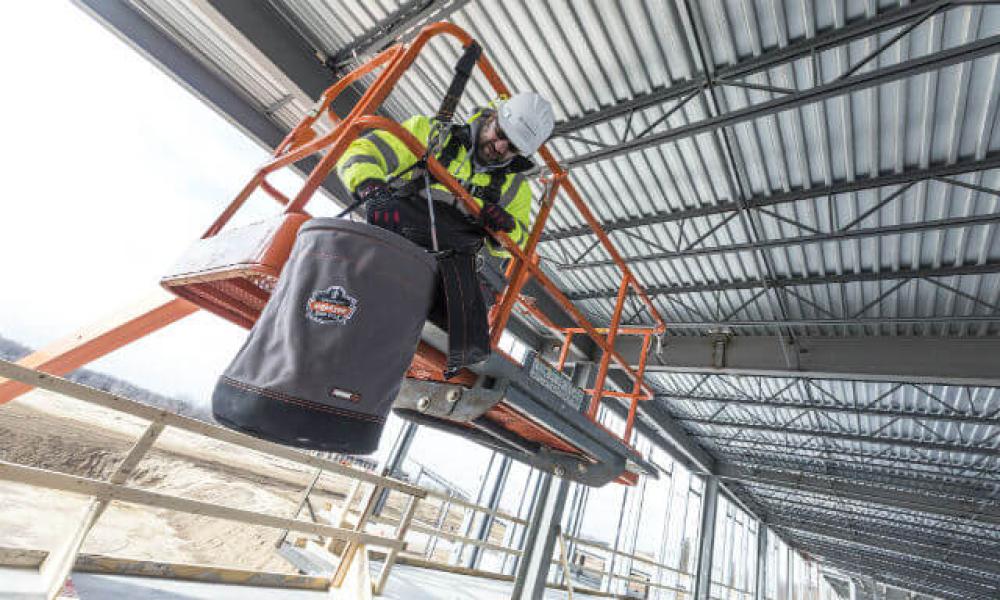
If hazards cannot be eliminated or substituted, fix unsafe conditions around your worksite by establishing engineering controls. Utilize passive engineering controls, such as toe boards, netting or barricades. Also, establish active engineering controls using the 3T’s (tethering, trapping or topping) to address unsafe conditions that can’t be fixed.
Implement administrative controls like policies and procedures, training and spreading awareness. Establish zones to require certain forms of PPE and administrative controls (i.e. Red Zones must use tool tethering and PPE; Yellow requires PPE only; and green are safe zones where neither is required).
Even though it is a last line of defense, PPE procedures must be established as well. Wearing hardhats, protective shoes and eyewear might seem like second nature, but make sure they are part of your entire plan.
Policy Creation
After your pilot study has concluded, summarize your findings and freeze the processes you’ve put in place. This will be the foundation of your Objects at Heights Policy. Have your champions refer to a sample Objects at Heights Policy as they write yours. There are plenty of useful templates to reference out there. Download our Objects at Heights Sample Policy Here.
A complete policy should include:
- Introduction
- Scope
- Responsibilities
- Hazard Analysis, Risk Assessment and Task Planning
- Worksite Inspection
Tedious though it may be, being thorough on the front end of your implementation will prevent you from having to go back and redo steps. And putting that policy in writing will give you (and your employees something to refer to (and will ensure your liability). A good policy should be firm yet flexible enough to allow for improvement happen in real time. Most importantly it should be something that everyone understands and agrees to abide by.
Our four-part series will conclude with a post on launching your dropped objects prevention program, and how to review and expand it. Read Part 4 now.